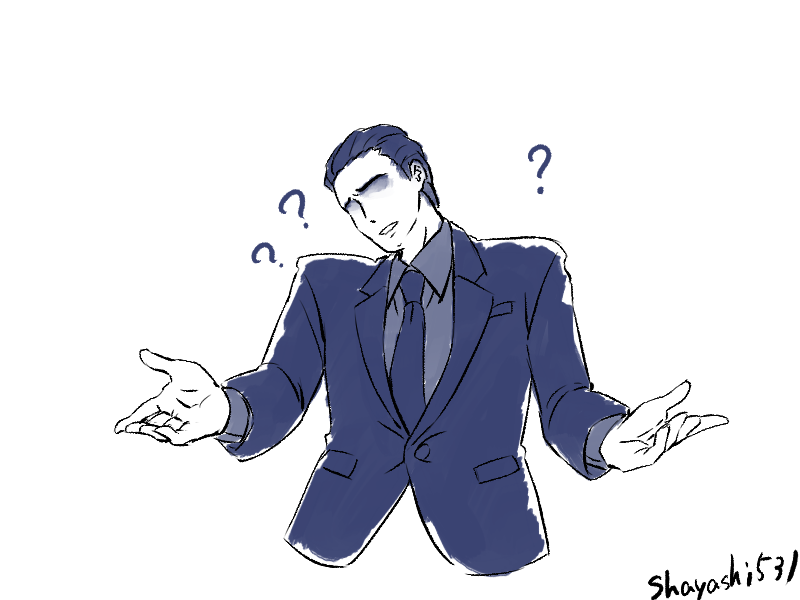
昨今のDX(デジタルトランスフォーメーション)がビジネスの各シーンでキーワードとして使われています。セットメーカー様の中には新製品設計において既にDXを導入・実践中というところもあるでしょう。製品設計に関わるツールの類については常に最新のものが各ベンダーより提案され、メカ設計・エレキ設計を統合したCAD設計の環境も完成されつつあり、いわゆる”デジタルツイン”の実現もそれ程遠い将来ではないかもしれません。
そういった中で新製品設計におけるEMC設計はどうなのでしょうか?理想の状態としては、”デジタルツイン”により、製品に関するEMC性能をデジタル環境の中で事前に評価して製品が実際に製造された際にはEMC課題がすべてクリアされている、ということになるのでしょう。
しかしながら、EMCのようなノイズ課題解決が設計する製品にどれだけの付加価値、即ち製品のエンドユーザーにとってどれだけの価値を提供できるか、を考えた時セットメーカーとしてはEMC課題に対する設計ツールのコスト、そのツールにデータを入力するための設計システム運営上の変更、ツールのオペレータの確保、またオペレーションに掛かる時間等を考慮すると、やはり費用対効果の低さと工数時間のロスによりEMCを”デジタルツイン”の範疇にすることは考えないでしょう。(大概の製品はそのEMC性能に関係なく設計仕様の性能を出せる。)そもそもノイズの課題についての解析・予測については複雑な要因が関係するため、今の学術レベルのアプローチを以ってしても完全な事前設計は難しいのが現状です。
現在、ツールベンダーからはEMC設計に関してSI、PI評価を基にしたEMC設計向けのツールとか、回路基板(プリント基板)の配線設計に対するEMCルールチェッカーが提供されていますが、実際はできたもの(CADデータ)に対する評価という性格が強く、設計する製品に関するEMC、特に不要輻射(EMI)に対して十分な評価をしていない(できない)のが実状です。結局、チェックはしたけれど実際に作ってみないと分からないといったところです。従って、現在のEMC設計はDXしていたように見えて、実はDXまでには至っていないと思われます。
少なくとも、SI、PI評価が設計する製品のEMC評価に繋がるものであるべきと考えます。当社の”SD適用”、”PD適用”はSI、PI評価をそのメカニズムからEMC評価に関係付けます。そして、不要輻射(EMI)低減のために如何なる設計をすべきかをアドバイスします。これらの詳細につきましては、是非当社にお問い合わせください。
関連ページ