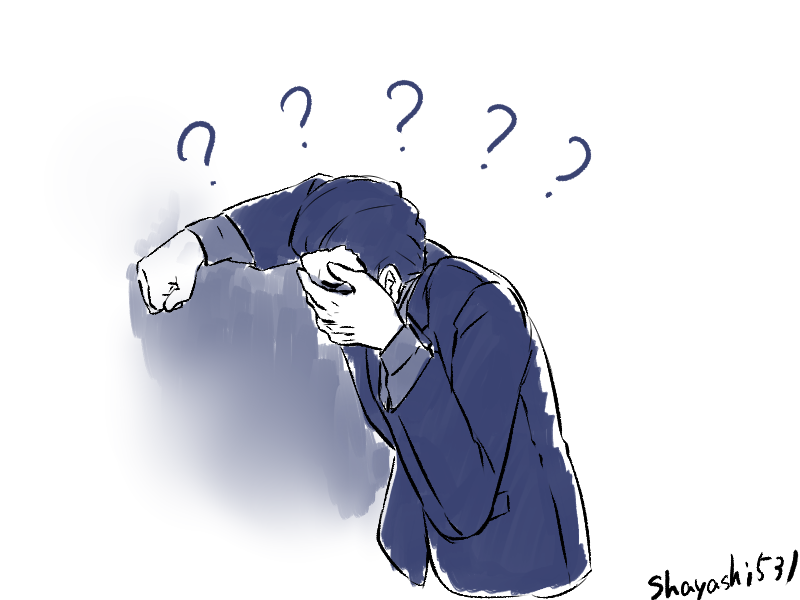
電子機器から放射されるノイズ(不要輻射・EMI)対策としてEMCノイズ対策部品としてのフェライトコアはEMC技術者にとって、最も期待できる定石の部品ではないでしょうか。EMI対策としてフェライトコアが対策箇所にマッチすると、放射ノイズを10dB以上低減でき、EMI対策を担当したEMC技術者にとっても晴れ晴れしい気持ちになるでしょう。
しかしながら、EMCノイズ対策部品としてのフェライトコアは電子機器を設計するメカ担当者からするとあまり歓迎できない部品なのです。先ず部品として形状が大きく且つ重いため、ただケーブルに通してブラブラさせておくことができない(特に可動性のある部位等)ので、保持し且つ電子機器の筐体に固定させるためのフェライトコアのホルダーも用意しなければならず、部材の準備と手配、更に製品製造時の組付け作業等で費用がかかるので、できれば使用して欲しくないEMCノイズ対策部品なのです。
また、フェライトコアはコア自体の体積がEMI低減効果に影響します。即ち、大きなコア程EMIを低減する効果があります。コアの材料としても材料メーカーならどこでも製造できる安価なフェライト(Mn-Zn系/Ni-Zn系)です。20年位前の国内のEMCノイズ対策部品メーカー(材料メーカー)ではよりEMI対策効果が期待できる高性能なフェライト材料の開発が行われていました。しかし、コスト意識の高いセットメーカーにとっては大きくなっても安いフェライトコアを求めた結果、現在では海外のものが主流となっています。
フェライトコアでEMI対策できる周波数帯は30MHzからせいぜい300MHz位でしょうか。300MHz以上の帯域では殆どEMI対策効果はありません。これはフェライトコアの材料としての磁気特性によるものです。また300MHzと言っても小さなコアではEMI対策効果は殆ど期待できず、コア形状を大きくすることで小さくなっていく対策効果を保持させます。また、ケーブルを複数回フェライトコアに巻き付けてEMI対策効果を補強します。このようなケーブルのコアへの巻き付きも手作業で行うことになるので、生産数量の多い製品では避けたい方法です。
一方、EMC技術者の中には、フェライトコアにより非常によいEMI対策が得られた場合と、そうではなかった場合を経験されていると思います。これについて業界の文献やハウツー本では、ノイズがケーブルにコモンモードでのっていれば効果があり、ノーマルモードの場合は効果が低い、等と説明されたりしています。確かにそのように見えますが、実はどちらもノイズはノーマルモードで伝搬しており、もっと違うところに原因があると、私は考えております。またフェライトコアのEMI対策効果を十分に発揮させる上で、フェライトコアのケーブルにおける装着位置も極めて重要な要素です。こういったフェライトコアに関する詳細については当社の”EMC設計・背景説明”の中でご説明致します。
そもそもフェライトコアを使わずに済んだら、機器設計関係者から生産工程の方々、そしてお金を払って製品を買っていただくエンドユーザー様までいろんな意味で負担が軽減されます。(EMCノイズ対策部品メーカーには好ましくないかな)このフェライトコアを使わず済ませる設計方法が、当社のEMC設計、”PD適用”、”SD適用”です。ご検討のほどよろしくお願い致します。